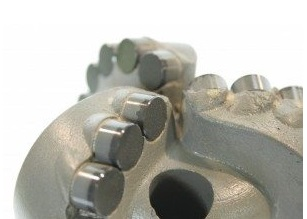
PDC- ODER PKD-BOHRER? WAS IST DER UNTERSCHIED?
PDC-Bohrer bedeutet Polykristalliner Diamantschneider-Kernbohrer
Die frühesten Brunnen waren Wasserbrunnen, flache Gruben, die von Hand in Regionen gegraben wurden, in denen der Grundwasserspiegel die Oberfläche erreichte, normalerweise mit Mauerwerk oder Holzwänden, die den Brunnen säumten.
PDC werden hergestellt, indem einige Schichten aus polykristallinem Diamant (PCD) mit einer Schicht aus Hartmetall bei hoher Temperatur und hohem Druck kombiniert werden.
PDCs gehören zu den robustesten Materialien für Diamantwerkzeuge.
PCD bedeutet einfach „Polykristalliner Diamant“: PCD wird normalerweise durch Sintern vieler Mikro-Einzeldiamantkristalle bei hoher Temperatur und hohem Druck hergestellt. PKD hat eine gute Bruchzähigkeit und eine gute thermische Stabilität und wird zur Herstellung geologischer Bohrer verwendet.
PDC bietet die Vorteile der hohen Verschleißfestigkeit von Diamant und der guten Zähigkeit von Hartmetall.
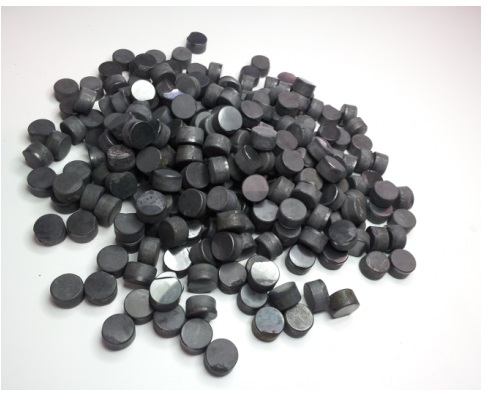
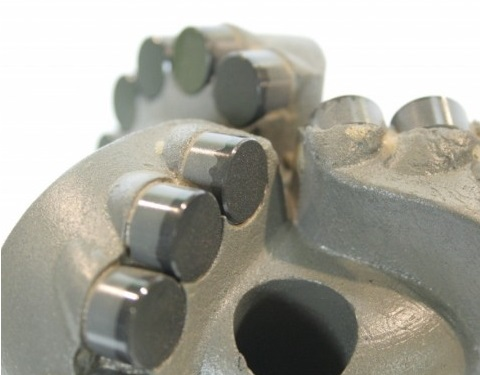
Wir liefern PDC-Bohrer, die mit einer Reihe geformter Schneiden oder polykristallinen Diamantpresskörpern (PDC) hergestellt werden, die auf einen Körper gelötet sind.
PDC-Fräser bestehen aus Hartmetallsubstrat und Diamantkörnung. Hohe Hitze von etwa 2800 Grad und hoher Druck von etwa 1.000.000 psi formen den Pressling. Außerdem ist eine Kobaltlegierung vorhanden, die als Katalysator für den Sinterprozess fungiert. Das Kobalt trägt zur Bindung von Hartmetall und Diamant bei.
Generell gilt, dass große Fräser (19 mm bis 25 mm) aggressiver sind als kleine Fräser. Allerdings können sie die Drehmomentschwankungen verstärken.
Es hat sich gezeigt, dass kleinere Fräser (8 mm, 10 mm, 13 mm und 16 mm) bei bestimmten Anwendungen mit einem höheren ROP bohren als große Fräser. Eine solche Anwendung ist beispielsweise Kalkstein.
Darüber hinaus produzieren kleine Fräser kleinere Schnitte, während große Fräser größere Schnitte erzeugen. Großes Bohrklein kann zu Problemen bei der Bohrlochreinigung führen, wenn die Bohrflüssigkeit das Bohrklein nicht nach oben befördern kann.
(1) oder (2) Weiche und weiche, klebrige, gut bohrbare Formationen wie Ton, Mergel, Gumbo und unverfestigter Sand.
(3) Sande, Schiefer und Anhydrite mit weicher bis mittlerer Druckfestigkeit und durchmischten harten Schichten.
(4) Sand, Kreide, Anhydrit und Schiefer mit mittlerer bis mittlerer Druckfestigkeit.
(6) Mittelhart – höhere Druckfestigkeit mit nicht oder halb scharfem Sand, Schiefer, Kalk und Anhydrit.
(7) Hart – Hohe Druckfestigkeit mit scharfen Sand- oder Schluffsteinschichten.
(8) Extrem harte, dichte und scharfkantige Formationen wie Quarzit und Vulkangestein.
PDC-SCHNEIDSTRUKTUR
PDC-Bits mit sehr weicher (1) bis mittlerer (4) Formation haben eine vorherrschende Größe des PDC-Fräsers. Die PDC-Schnittstruktur wird wie folgt bezeichnet:
2 – dieser Bohrer hat hauptsächlich 19-mm-Fräser
3 – dieser Bohrer hat hauptsächlich 13-mm-Fräser
4 – dieser Bohrer hat hauptsächlich 8-mm-Fräser
PDC-Bits
Zeitpunkt der Veröffentlichung: 31. August 2022